Metal Casting
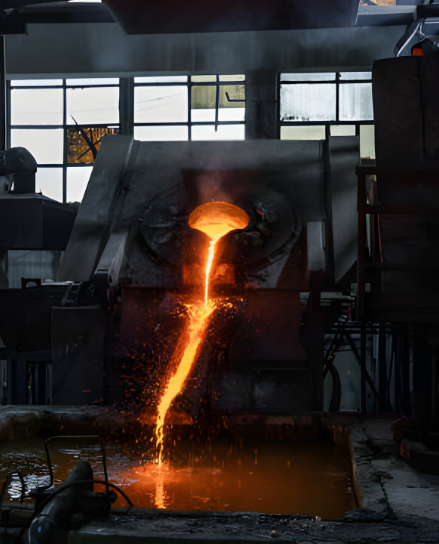
Metal Casting
Metal casting is a sophisticated manufacturing technique that involves melting metals and pouring them into custom molds to create intricate shapes, components, and parts. This versatile method caters to a wide range of industries and projects, providing exceptional quality, cost-effectiveness, and design flexibility.
Metal casting stands as a timeless art of crafting intricate metal components that bridge imagination and reality. Our state-of-the-art process melds innovation with tradition, allowing molten metal to take the shape of your designs. From ornate sculptures to industrial components, metal casting materializes the extraordinary.
Benefits of Metal Casting:
Precision Craftsmanship: Metal casting allows for the creation of highly intricate and complex shapes with remarkable precision, ensuring that each detail is faithfully reproduced in the final product.
Diverse Material Options: This method supports a vast array of metals, including iron, aluminum, bronze, and more. The choice of materials can be tailored to meet specific project requirements, such as strength, conductivity, or corrosion resistance.
Durability and Strength: Cast metal parts exhibit exceptional durability, making them ideal for applications requiring robustness and longevity. They can withstand extreme conditions and heavy loads.
Cost-Effective Production: Metal casting is well-suited for large-scale production runs due to its ability to create multiple identical parts efficiently. This scalability results in cost savings per unit, making it an economical choice for various projects.
Design Freedom: The casting process allows for intricate and unique designs that might be challenging to achieve through other manufacturing methods. This freedom enables the realization of innovative ideas.
Limitations of Metal Casting
While metal casting is a versatile manufacturing method with numerous benefits, it’s important to be aware of its limitations and potential downsides:
High Initial Costs: Setting up casting equipment, creating molds, and handling molten metals can result in significant upfront costs. This can be a deterrent for smaller-scale productions or projects with limited budgets.
Surface Finish and Detail: Depending on the casting method, cast parts might exhibit surface imperfections like roughness or porosity. Achieving high levels of surface finish and intricate detailing might require additional post-casting processes.
Size and Weight Limitations: The size and weight of cast parts can be limited by the capabilities of the foundry equipment. Producing extremely large or heavy components might necessitate more complex and expensive casting setups.
Material Selection: While metal casting supports a wide range of materials, certain alloys or metals might be challenging to cast due to their melting points, reactivity, or other properties.
Lead Times: Preparing molds, melting metals, and cooling can contribute to longer lead times compared to some other manufacturing processes. This might not be suitable for projects requiring quick turnarounds.
Tolerances and Dimensional Accuracy: Achieving tight tolerances and precise dimensional accuracy can be challenging in casting, particularly for more intricate designs. Some level of variability might be present.
Limited Complex Shapes: While casting can accommodate a wide range of shapes, extremely intricate or complex designs might be challenging to achieve accurately through casting methods.
Post-Casting Processes: Depending on the casting method used, post-casting processes like machining, finishing, and heat treatment might be required to achieve the desired final properties and dimensions.
Consulting and Planning
In addition to our metal casting services, we also offer a range of value-added services to support our clients throughout the entire manufacturing process. At GDC Manufacturing, we understand that every project is unique and may require specialized knowledge and expertise. That is why consulting services to assist our clients in every step of the manufacturing process is included at no additional cost (minor exceptions apply). Our team of experienced engineers and machinists will work with you to evaluate your project requirements and provide expert advice on the best manufacturing methods, materials, and tolerances to ensure that your project is completed to your satisfaction. With our consulting services, you can have peace of mind knowing that your project is in good hands.
Our team of experts will work closely with you to understand your specific needs and requirements. We will then use our extensive experience and knowledge to develop a comprehensive plan that outlines the best approach for your project. We take into consideration factors such as project timeline, budget, and materials to ensure that we are able to deliver a finished product that meets your expectations and exceeds your requirements. Whether you are looking to create a one-of-a-kind prototype or to bring a new product to market, our team is here to help you every step of the way.
With our commitment to quality, precision, and customer service, we are dedicated to helping our clients achieve their goals and bring their ideas to life.
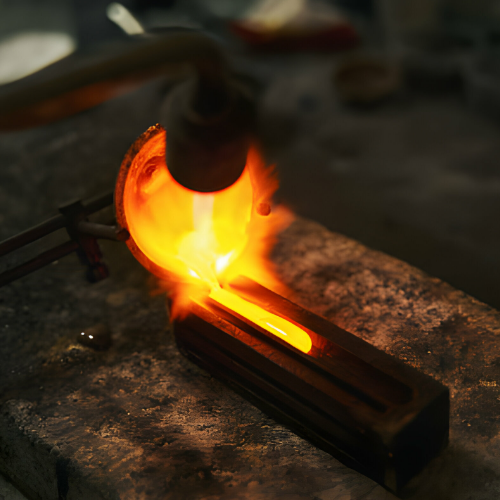

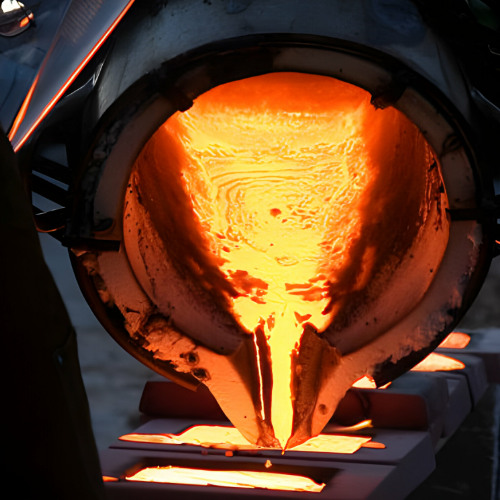
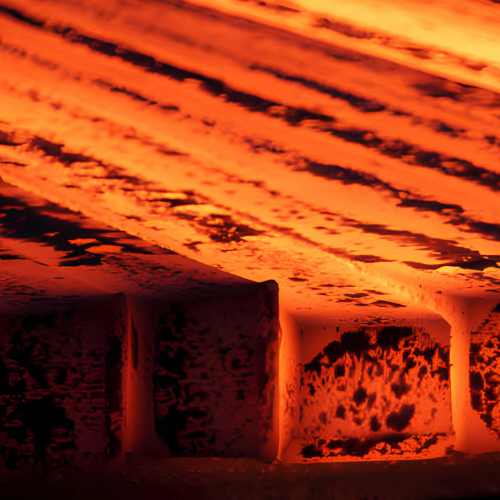